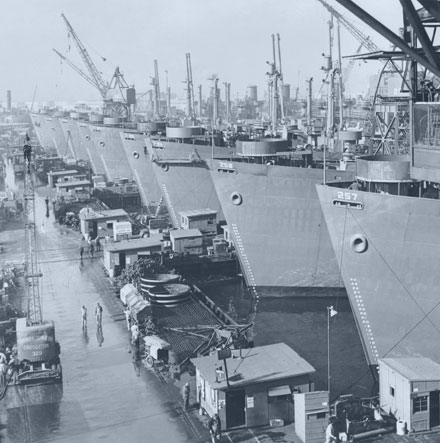
CAN LEAN BE FULLY IMPLEMENTED IN SHIPBUILDING?
Traditional-minded shipbuilders conceive LEAN as a system only applicable for semi-automated automotive assembly chains, since they envisage shipbuilding as a completely different activity (i.e. as a craft-evolving and project-oriented complex manufacturing process).
Despite, LEAN can be fully applied to shipbuilding process, provided some key functions are implemented or drastically improved in the shipyard, including:
-
Product development (in engineering stage).
-
Thorough application of Groups technology, or setting families of similar interim products and transform them under standardized processes (i.e. shifting to “product-oriented” operations).
-
Standardization of interim products (at least to a certain degree, specially for the upstream low-level products).
-
Modularization (specially for outfitting and E&I components).
-
Streamlined and parallel production of interim products.
-
Shifting work-control from “scheduling” to a PULL system…